Large Assembly Weld Cell
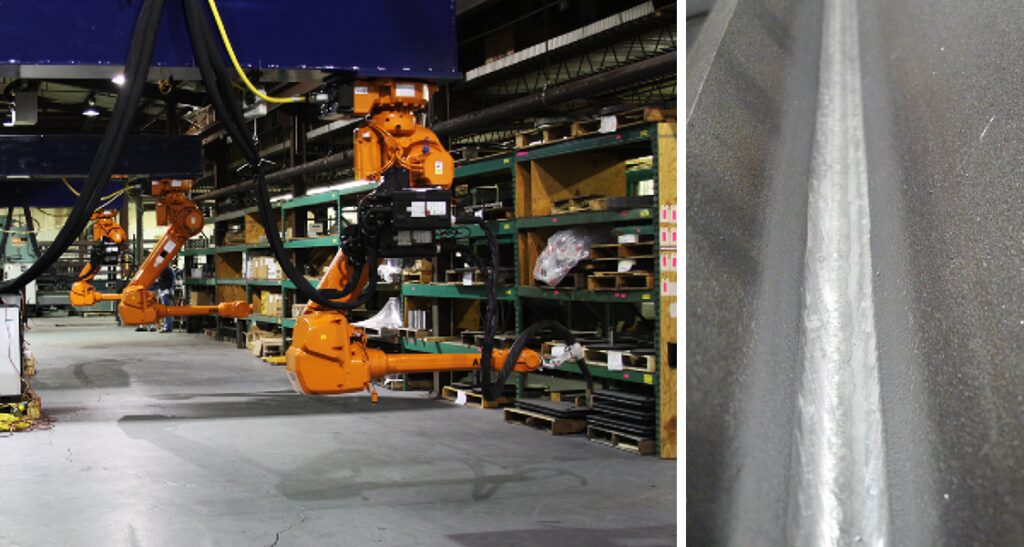
Project Detail
This custom weld cell utilizes six robots in a work cell measuring 140’x40’x30’. Three robots on each side of a column and boom system function to weld and clean oddly-shaped parts which each weigh 30 tons. The four robots on either end of the cell weld the part, while the two center robots, equipped with wire brushes, provide inter-pass cleaning. An engineered trunnion and clamp system lifts, rotates, and lowers the 30-ton parts. The project introduced twin pulse welding technology to the customer’s facility and required qualification of the process.

The Aim
Reduce production cycle time while improving weld quality, reducing rework and automating the material handling process.

The Outcome
Successful. Reduced the lifting, rotating, and lowering process that required 2 weeks to 4 hours. Reduced part manufacturing time from 17 weeks to 8 weeks.
“Navus provided a custom cell utilizing six robots to weld and clean oddly-shaped parts weighing up to 30 tons that reduced the part manufacturing time by 53%.”